Nailing Specs
The largest single reason to why a composition roof would fail prematurely is due to improper nailing. I can already feel the wrath of the roofers nation wide as begin to write this article.
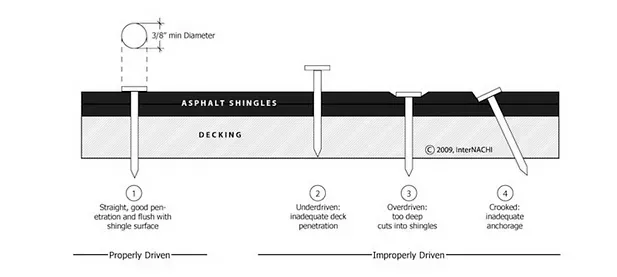
Why Nailing is King
The figure above shows properly driven nails and improperly driven.
Properly driven nails are perpendicular to the roof surface and the nail head is clamping the material tight to the deck.
When a nail is under driven it isn't clamped to the roof surface. The shingle is hanging on the shaft of the nail instead and with drag load from snow, the weight will cause the shingle to slide down the slope. The nail will not move and as a result the shingle will be sliced as it move downwards.
When a nail is over driven it has broken through the material. The nail head doesn't have very much material if any to clamp the shingle down to the deck. As a result these shingles can slide down from drag load or be lifted away by wind.
When a nail is driven at an angle or crooked this nail head isn't fully clamping the shingle down to the roof deck with the entire surface of the nail head, but at this point this is the least of the concerns. Crooked nails tend to back up out of the substrate. The result is that the nail head will poke through the shingle that is cover it and put a hole in your roof system. Below are a few pictures of what this looks like.
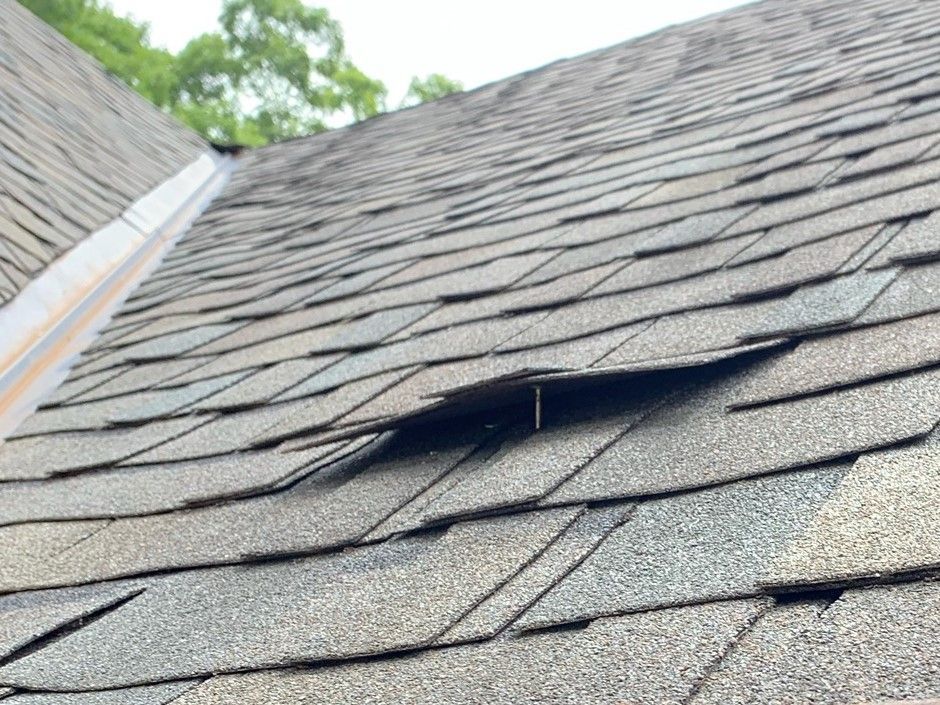
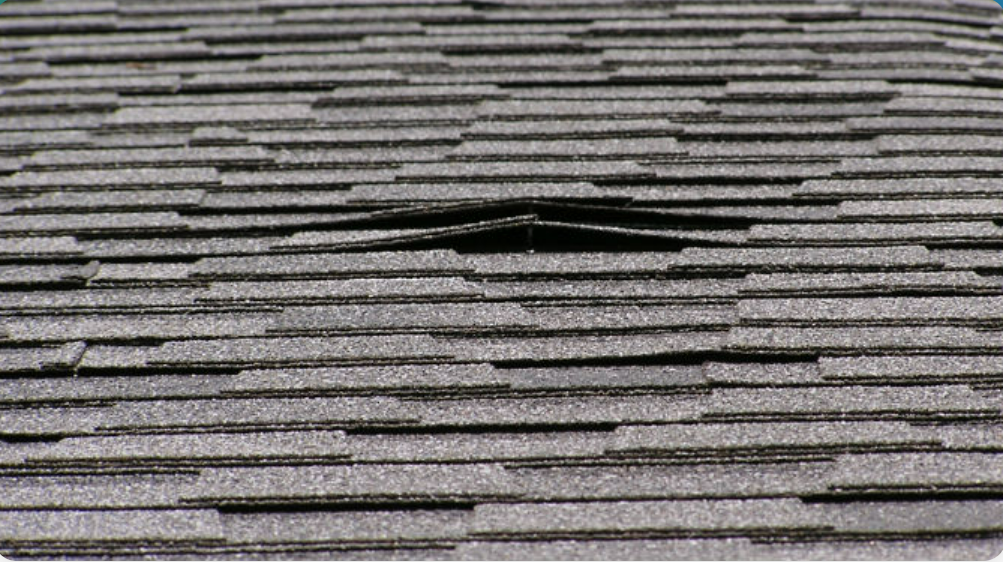
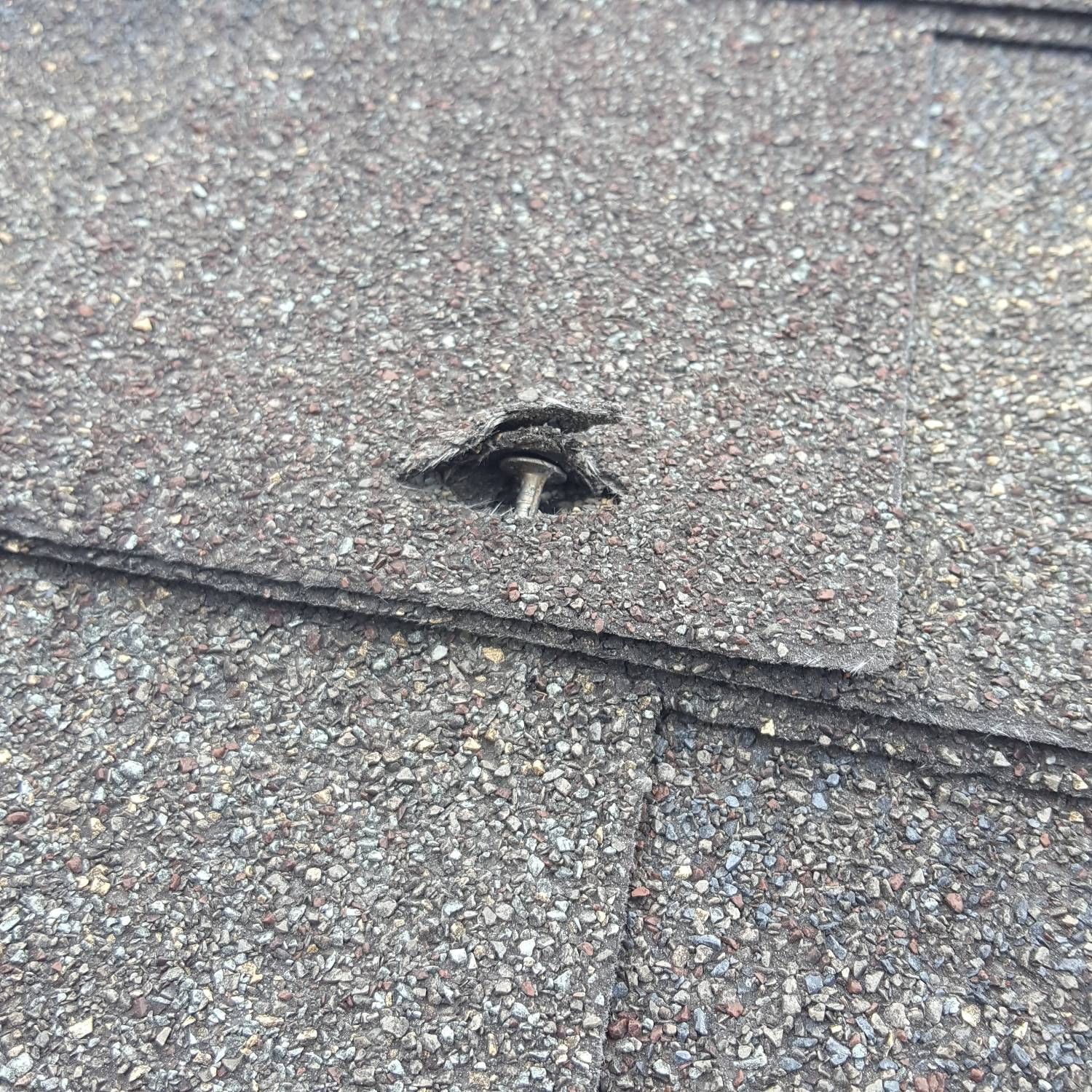
The fix for each of these is simple. The gun's pressure needs to be adjusted up or down to drive the nail harder if it's under driven and less if it's over driven. We see under and over driven nails all the time when we do repairs and we believe that the gun's are not being adjusted. It is possible that the installer will adjust his gun once when he begins working and then never looks back. So lets say they begin early in the morning and the gun is over driving the nails, they will release the pressure and now the nails are driven perfectly. But as the temperatures rise the shingles warm up and get blistering hot now the nails are blowing through the softer material.
Slowing down is the second fix. The reason why slowing down could mean all the difference in the world is that the installer might see that the nails are over driven and change the settings on the gun. But there is a major issue with this simple and perfect solution.
Piece Rates Roofers are prideful things, they pride themselves on being able to withstand harsh temperatures work in harsh conditions and most of all boastful of how FAST they can roof. Search YouTube and you will find many proudly claiming to be the fastest roofer. I cringe when I see them fly.
Piece rates are a form of paying an installer for production, not quality purely production. Its wonderful for the contractor when the roof is installed at break neck speeds, but terrible for the customer. Like a Rodeo the job was started and finished in a flash, they throw up their hands as if they roped a speeding calf and tied it's legs in 9 seconds. Yes they beat all sorts of records and they proudly walk the home owner out to the street to admire the work. The home owners eyes light up, a job well done at an amazing price, this must be praised on all the big sites.
"Five star service, these boy's showed up every day, took them only 2 days to complete the project at a good price too! They are polite and helpful, we just can't rave enough about Contractor X."
As we always say, anyone can make it look good from the street, the devil is in the details and trust me the devil will come knocking soon enough! Are these reviews every removed when the roof starts to fly off? What about the five year workmanship? Well the truth is premature roof failure doesn't happen right away. Most of the time its after the first ten or fifteen years that these issues begin. Now I have seen major disasters after two years where the entire roof was riddled with holes from nails backing up, but that was only once that I've seen that.
Piece rates are terrible because the contractor pays the installer X amount of dollars for every square, or 4 bundles installed. This means in order to make a good wage they have to fly. The other reason why piece rates are terrible for home owners is because these professionals love open areas to roof where they can make money installing. However the un-experienced workers who have little to no training are placed on the details.
Piece rate employee's suffer the lack of training, no one has time to teach them since they are all too busy making the big bucks. So the piece rate installer is stuck trying to figure out how to do the job. And because roofing is considered seasonal work most contractors lay off the entire work force after Thanksgiving so many of these employee's find winter work. The roofing industry has a high turn over rate of employee's and it's most contractors pay piece rates so the industry is saturated with under trained installers who have learned to install every way but the right way.
"Every roofer has his own way". This is something we hear a lot in the industry, and it's true. Each roofer has figured out how to do certain things a certain way and they never deviate from that method. Many installers will argue about whos' "WAY" is better.
The installer who is paid piece rates typically fire a nail every half a nano second and as the last nail is being fired the next shingle is already being slid into place.
https://youtu.be/Y4Dpt38UUVs?t=80
At time2: 26 He says, "With my eyes closed". At 2: 30 You can see that he nail too low as he installs the next shingle, this exposed nail is called a shiner and will rust over time. The photo below shows the silver nail head remain exposed as he nails the shingle above in place.
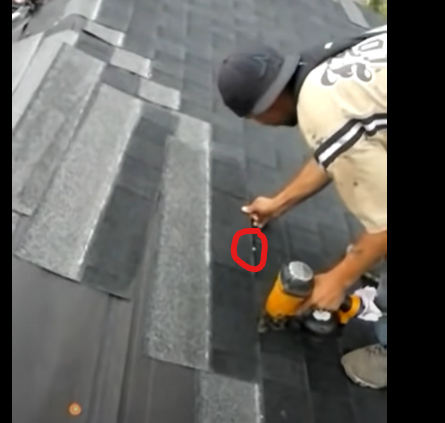
Did you see how fast he is nailing and what he said? "On the line every time." He might be hitting the nail line but he never looks at the nails he installed, he moves on. Consider that he is using 1 1/4" coils and I know they travel down the nail shaft and bounce around, so not ever nail is going to come out as straight as an arrow. This is why Yakima Roofing & Remodeling, LLC uses 1 3/4" coils, the longer nails travels straight down the shaft and enters the wood straight.
The problem with nailing so fast is that the installer nails with his gun tilted at a slight angle. Each nail is placed crooked according to the manufacture nail specs. Because of their amazing speed they have 0 time to check each nail to see if it was installed according to spec. All they are looking for is, "On the line every time." And that's just in this installers case.
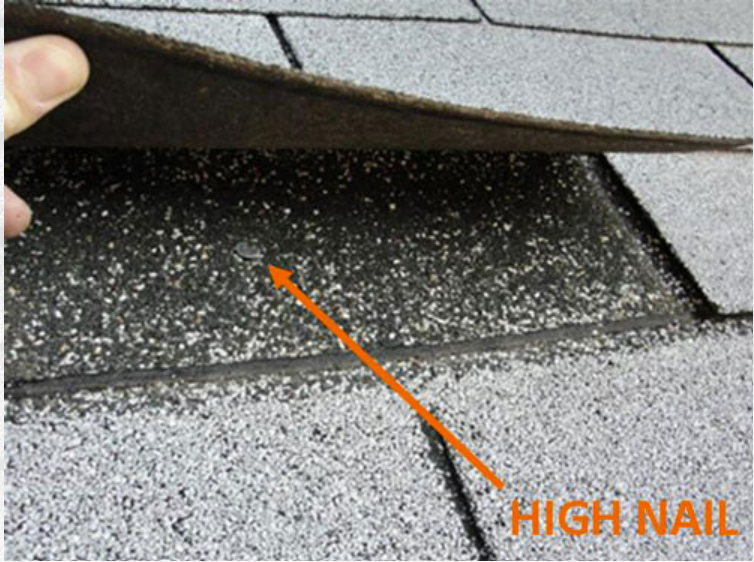
Many installers nail too high and miss the nail line by an average of 1". Many nail 2" too high while others nail 1/2" too high. Either way the nail is being placed in the thinnest part of the shingle. To make matters worse they are nailing too far up the shingle so even if the nail was correctly placed flush and straight it doesn't have much to hold down and the wind can easily lift the shingles away.
In this Video you can see that his nailing is close to the line and in the comment's everyone sing's praise to how amazing he is.
However looking closely you can see that his nails might be close to the line, but they are not withing 1" of the shingle edge according to many manufactures it's closer to 2" away. Small detail but lets move on. Some of his nails are driven above the nail line some ever so slightly but this is the weakest part of the shingle. From what I can see a hint of darkness around some of the nails indicates that the nails have blown through or broken the surface of the material.
Can these installers account for every nail they've driven? No! They pride themselves solely on their speed and as a result roofs blow off all over town. The solution is the bane of the piece rate installer the solution to the piece rate installer is faster is better it literally equals more money in their pocket and it means that the contractor get's the job done sooner and can move on to the next poor customer on their list.
Hourly wages means that installers can slow down, take time to teach new installers the manufactures installation specs. Hourly wage workers enjoy greater training and the customer unknowingly benefits with a better install at a fair market price. But even if the installers are paid an hourly wage they will tend to want to speed up, I guess it's just in the blood.
At Yakima Roofing & Remodeling, LLC we teach our installers to work at a constant work pace where they can inspect each driven nail to make sure it passes the manufactures specs. Our installers are taught how the manufactures want's details completed and don't try to figure out their own ways of doing things.
A detail that isn't done correctly can be fix, however an entire roof that wasn't nailed correctly must be re-roofed. Why is nailing King? The manufacture will void your new roof's warranty if the nailing isn't done according to their specs.
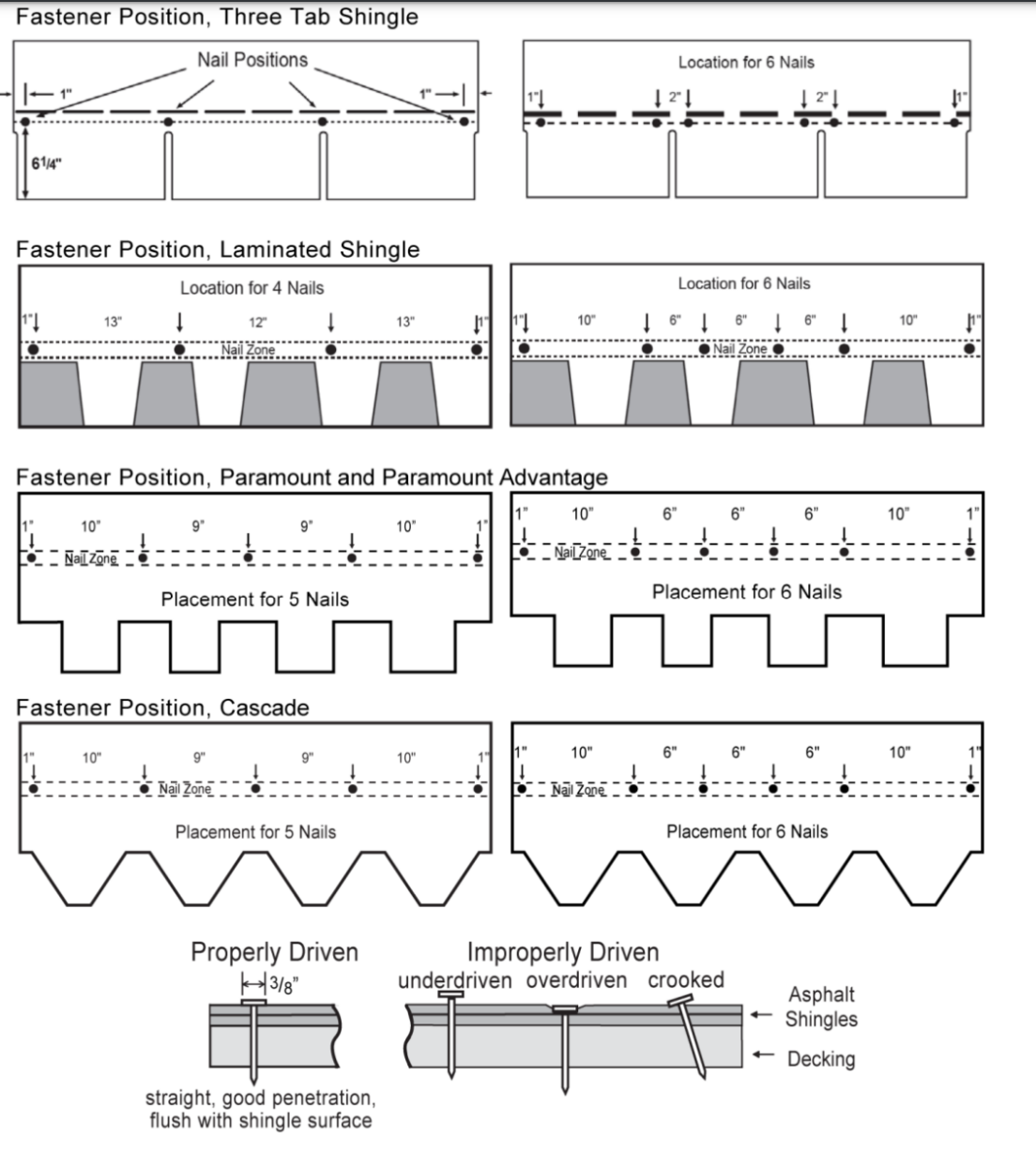
If your shingles develop a defect half way through their life and you call the manufacture. Your warranty depends on if the nailing specs had been achieved or not. If the nailing is done according to specs you would be given a new roof and paid by the manufacture to have it installed. If your nailing specs are not done according to specs you would have to pay for a new roof out of pocket.
Now watch those video's again, would you want to put your warranty on the line for someone's pride? Because they want to look good doing the job? So they can get your money in their pockets faster?
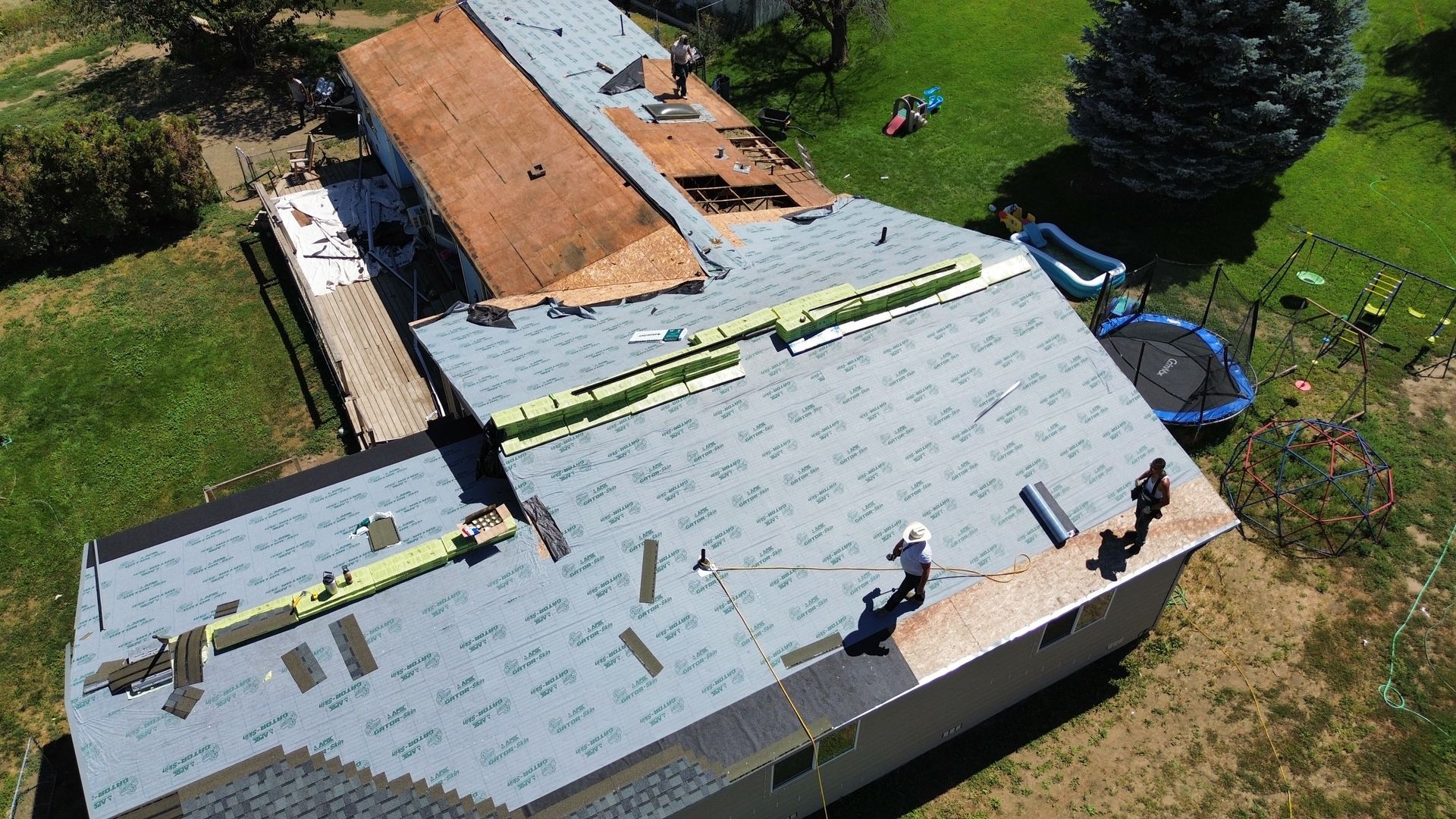
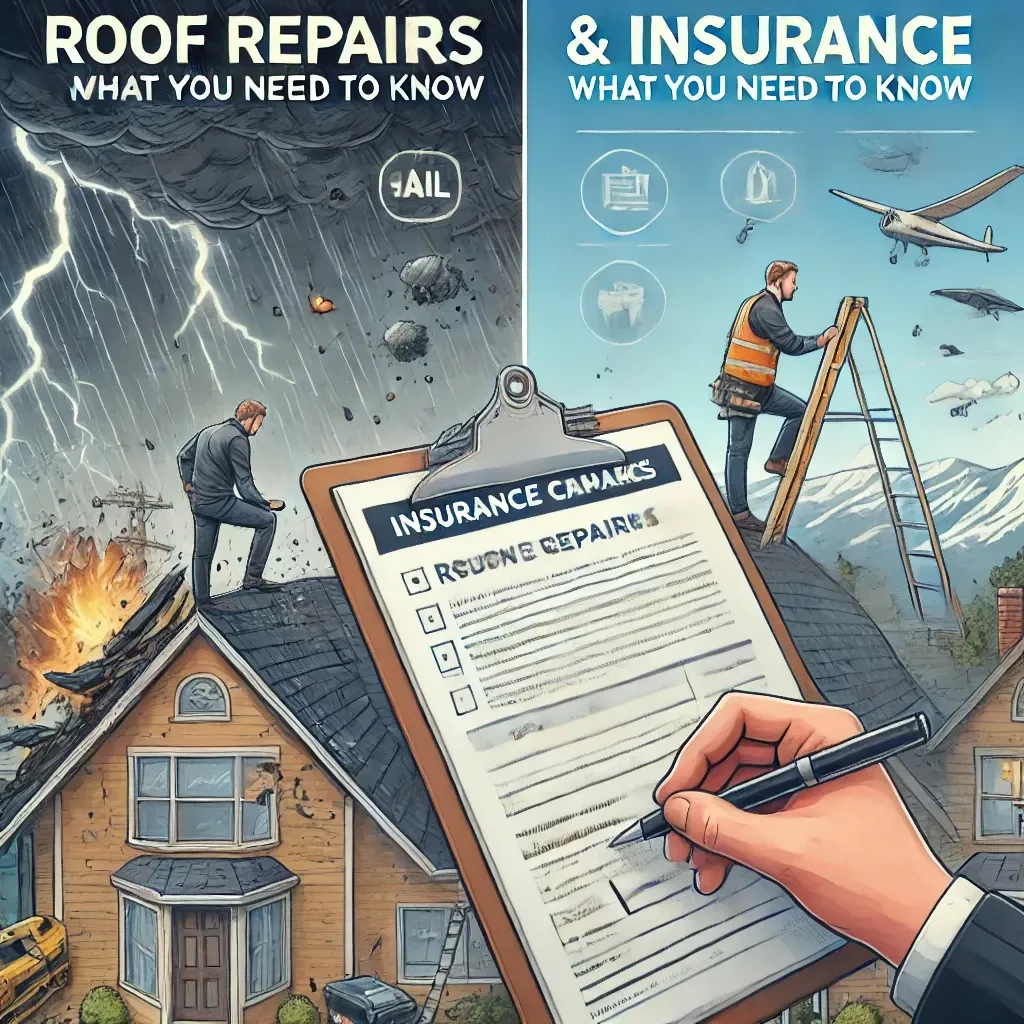
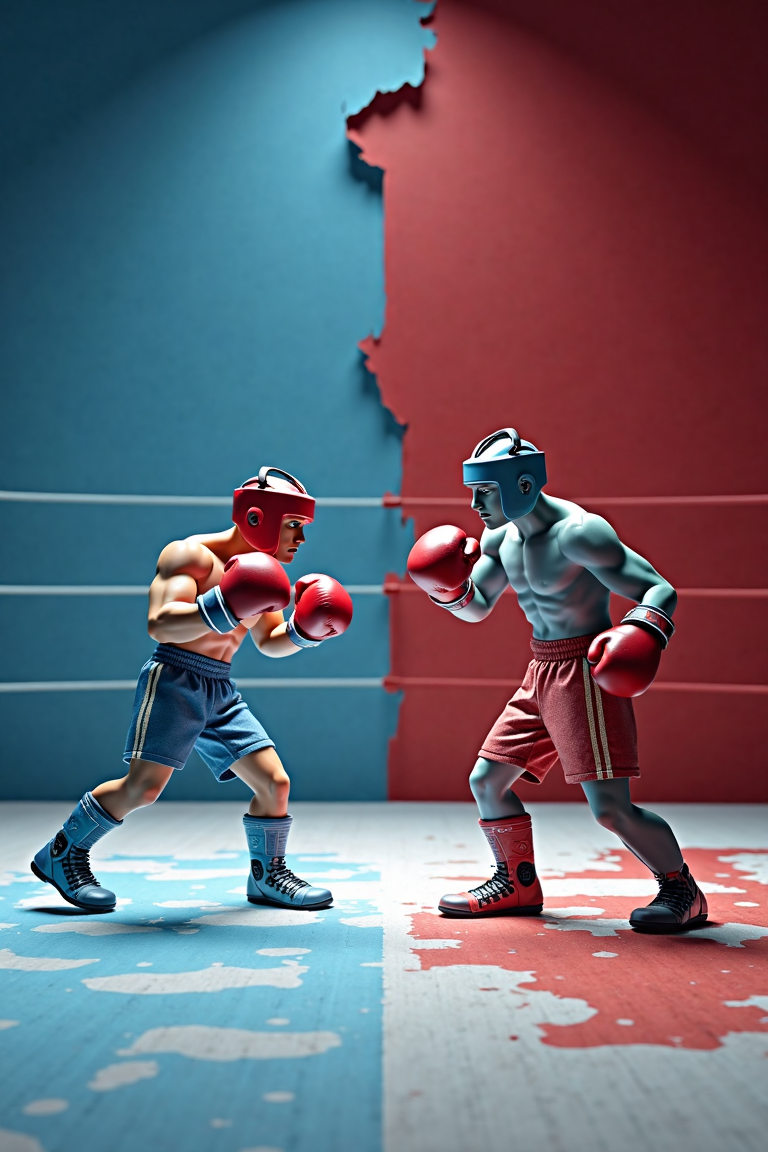
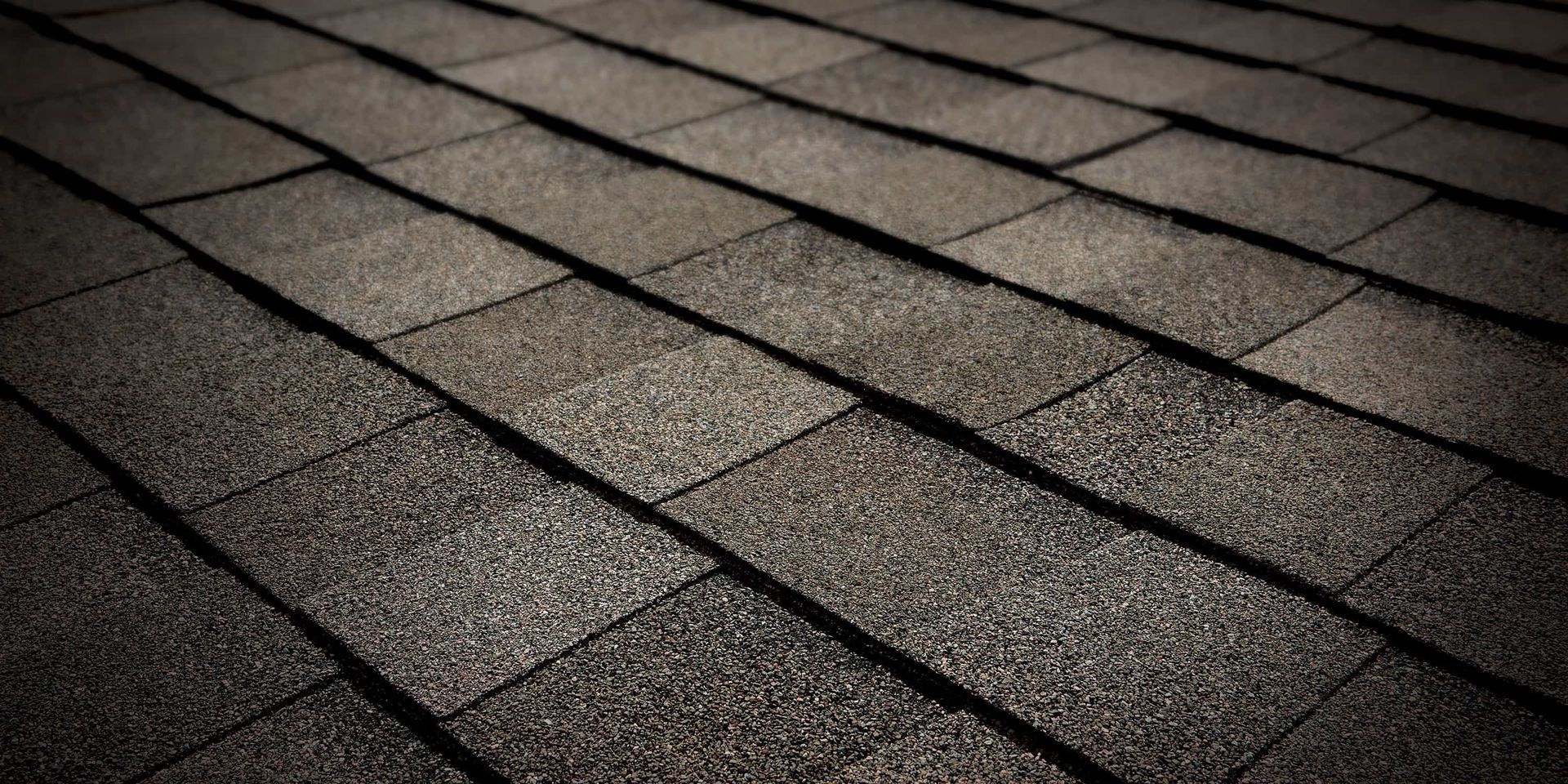